Flint Hills Resources – FHRCC 2021 Turnaround
Location: Corpus Christi, Texas
- Duration: January 2021 – February 2021
- Workhours: 140,000
- Percentage of Labor Self-Performed: 80%
- OSHA Recordables: ZERO
- Contract Value: 5.5MM
- Subcontractors: 5
project quick facts
Turner’s scope for the FHRCC 2021 Turnaround included scaffolding, insulation, painting and abatement.
Scaffolding: Erected 979 scaffolds throughout the duration of the Turnaround event.
Insulation: Installed approximately 26,000 square feet, and 3,350 linear feet of insulation.
- Approximately 23,000 square feet of installed insulation was in the FCCU 01DC102 Reactor.
- Approximately 3,000 square feet of installed insulation was in the ALKY 03FA363 Second Stage Acid Settler vessel in the acid area fully dressed out in acid protective suits.
- Of the 3,350 linear feet of insulation installed was covered between 167 work scope packages in the ALKY, and 66 work scope packages in the FCCU units.
Painting: Wet & Dry Blasted, power tooled, hand prepped, & coated approximately 2,000 square feet, 936 welds, and erection marks in various sizes of pipe.
- Approximately 23,000 square feet of installed insulation was in the FCCU 01DC102 Reactor.
- Approximately 3,000 square feet of installed insulation was in the ALKY 03FA363 Second Stage Acid Settler vessel in the acid area fully dressed out in acid protective suits.
- Of the 3,350 linear feet of insulation installed was covered between 167 work scope packages in the ALKY, and 66 work scope packages in the FCCU units.
- Approximately 322 welds and erection marks in the FCCU unit ranging in sizes from 24” down to ¾” piping.
- Approximately 614 welds and erection marks in the Alky unit ranging in sizes from 28” down to ¾”, with majority of this scope of work in an acid area. Fully dressed out in acid protective suit.
- Exterior vapor blasted & coated 2,000 square feet on a vessel inside an Alky Unit acid area. Fully dressed out in acid protective suit.
Abatement: Lead abated approximately 350 square feet of structure steel, and piping.
Planning: Planned SIPA labor, materials, and equipment needs for the ALKY, and FCCU Turnarounds.
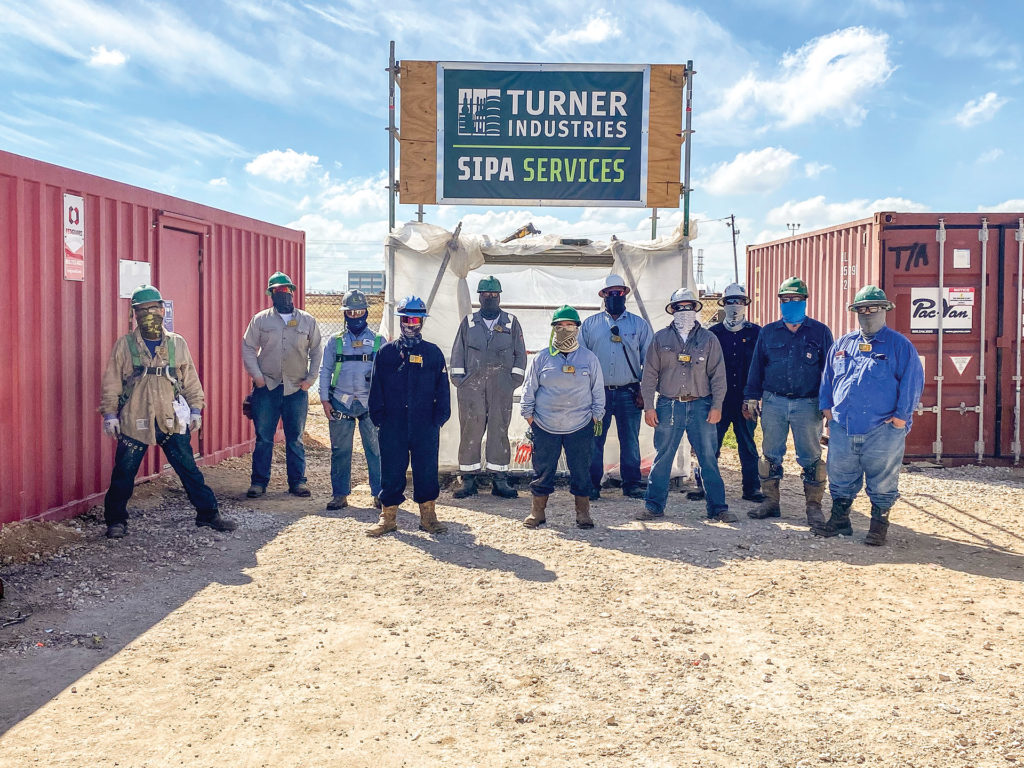
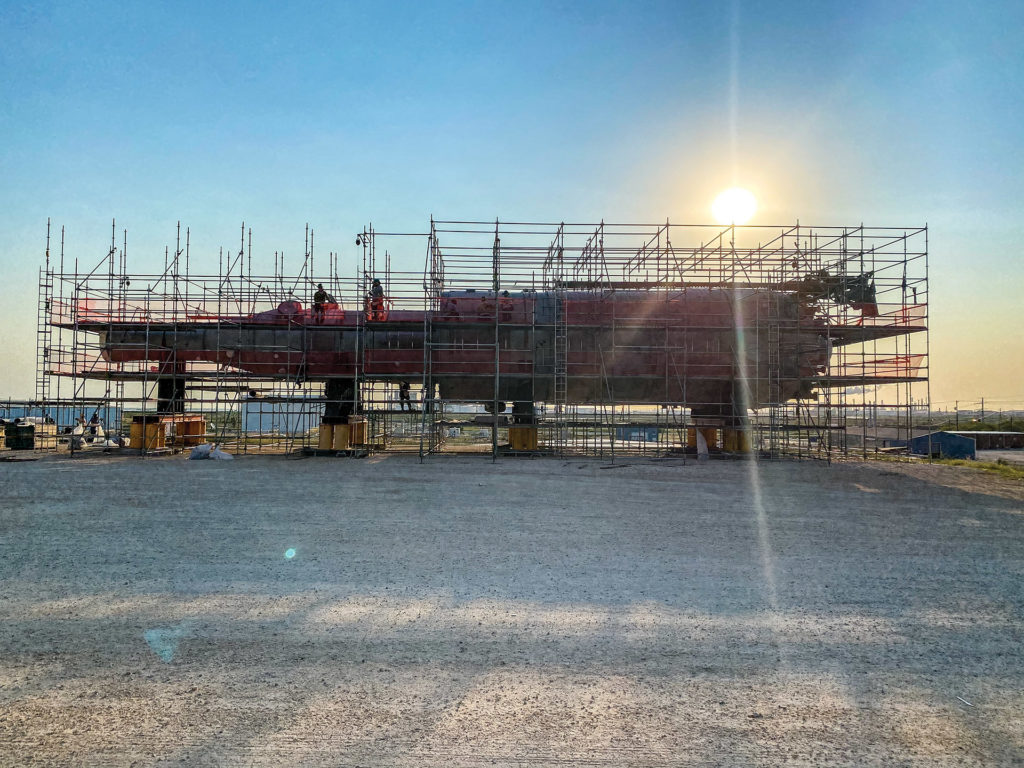
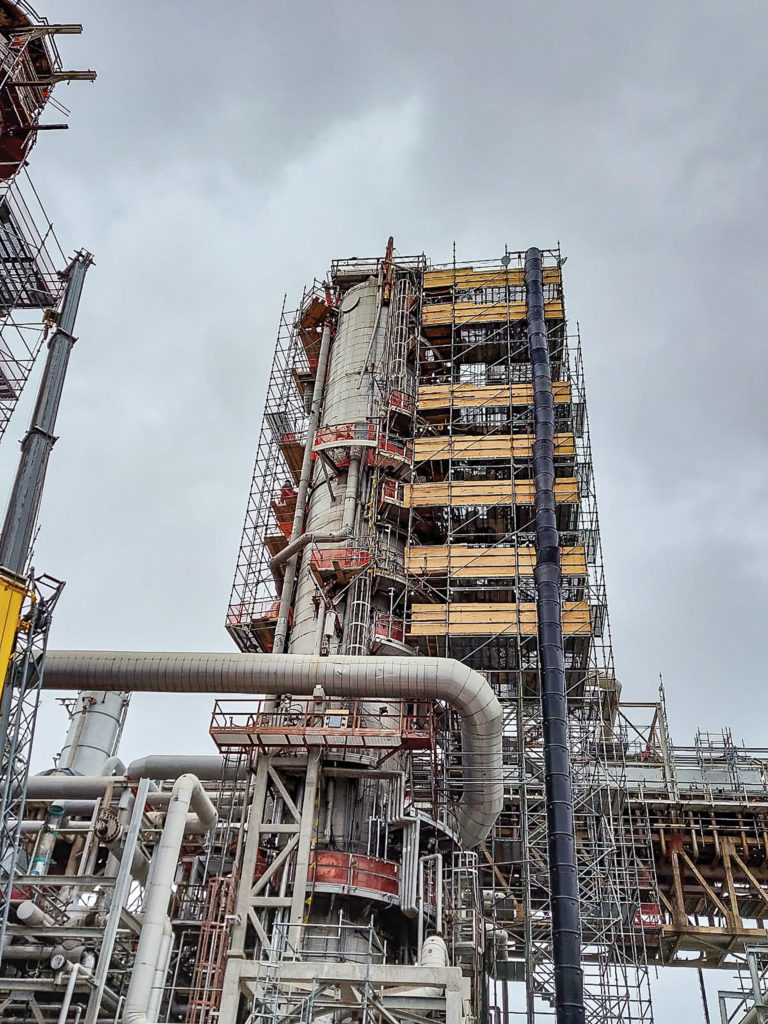